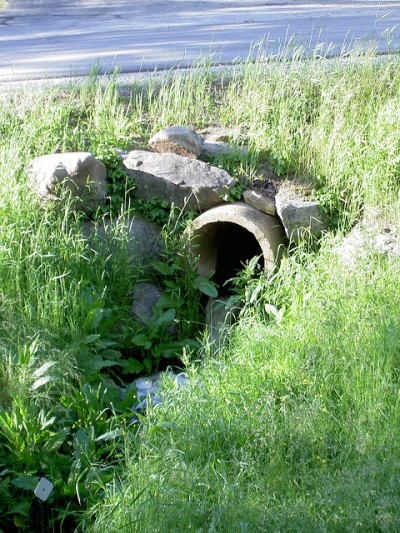
On June 9th and 10th, our engineers were invited to attend the Low Impact Development seminar. During the two-day survey, attendees not only learned about LID and the performance policy implication in Ohio, but also about bioretention design, construction, and maintenance.
Bioretention areas are landscape features that store and treat stormwater runoff on development sites. Commonly, these features are located in or around parking areas and, less frequently, in residential neighborhoods. While they are used to store and treat stormwater, this landscape architectural feature is not considered a stormwater wetland.
Design
One particular design discussed at the seminar was for soils that are suitable for infiltration. In these areas, it is possible to construct an undertraining system, which can be modified for infiltration. In this system, the pipe is installed near the top of the deep gravel layer. This creates a “sump” that collects and stores water for infiltration.
This is just one example out of the four bioretention design concepts considered most useful to Northern Ohio. To choose the best design, soil testing is advised. While soil maps help to indicate the dominant soil in a given area, trained scientists can tell builders the specifics about the properties and soil makeup. Armed with this information, we can choose the best bioretention design based on the unique properties and stormwater runoff needs of a specific area.
To pick the perfect site, many factors need to be considered, including site slopes, drainage area, bedrock, floodplain and wetlands, base flows and chlorinated flows, stormwater hot spots, and aesthetics. Before construction begins, all contributing drainage in the area needs to be stabilized.
Construction
Inspection of the site should start during construction. This includes testing of the soil mix and infiltration design. After proper testing, the site should be evacuated to exact dimensions. The evacuation technique will depend on the design chosen. Tilling tools are then used to refracture the soil structure and prepare the site for the underdrain pipe. The bioretention wells/cleanouts will be placed into the site vertically, and then soil can be added in horizontal layers. The final step is plant installation, which helps ensure the integrity of this new bioretention area. After construction, the site should be inspected to ensure it is built to certification.
Maintenance
After the construction is complete, maintenance continues. For optimal performance, make sure the filter bed functions and drains at a proper rate. Maintaining all of the vegetation is also crucial for integrity of the bioretention unit. All pretreatment should be checked and drains should be free of clogs.
Proper bioretention construction and oversight means that an area will have pollutant removal mechanisms that are found in nature.
Special thanks to Dan4th Nicholas for the image of this bioretention area.